

Our plastic bag design and non contact hand opening style.
In our "SpiroWay Disposable" product.
Inofab Health
Product Owner of Spirometers
SEPTEMBER 2020 - MAY 2022, ANKARA
During this period, we tried to analyze the follow-up of our products on the market and user feedback. We tried to integrate stock and production tracking into an ERP system for the uninterrupted continuation of mass production. We tried to further integrate R&D and production in the Quality Management Processes that we aimed to develop.
The processes I contribute to;
Before the product is put on the market, to control the technical features and the compliance with the regulation.
Planning and monitoring interdepartmental R&D processes on the product.
Planning and monitoring department-based R&D processes.
Monitoring and measuring post-market customer feedback.
Measuring after sales service, maintenance and monitoring user needs.
Production planning and sub-fractions on an annual basis.
Control of the compliance of the production process with the regulation to be applied.
Control of production documents in the quality management system.
Control of R&D and Quality Management System documents.
USING ODOO ERP SYSTEM

We started to use the ERP system for stock tracking in finished products. We first tried to integrate this program called ODOO according to ourselves. Then we created the product versions in ODOO and started stock tracking.
COLLECTING CUSTOMER FEEDBACK

We used the Jira program to collect and evaluate customer feedback. With the automation we did there, every feedback automatically created a task in Jira. We were evaluating these tasks on a weekly basis as a team. We were giving feedback to customers.
VERSION TRACKING AND USING GIT
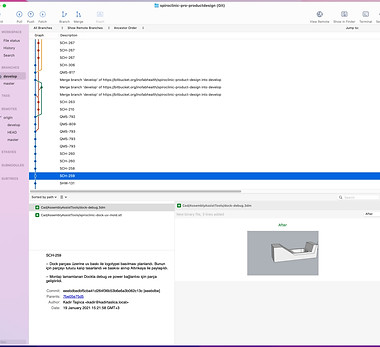
We used to track the versions of the parts we designed with GIT. We were committing and writing descriptions of each design version. This work later formed part of the "Design History File" work.
DESIGN HISTORY FILE

We created the Design History File, one of the most critical documents for the R&D and Quality Management System. With this document, we follow the development process of every piece we design and develop we could. Thus, we were able to track past improvement and change points for future design improvements of the part. It had been a long and challenging process for us.
TECHNICAL FILE CONTROL

We must ensure that the product technical file is always up to date and compatible with the product. For this reason, we used to create a checklist and check the entire technical file every 3 months. We were updating the technical file and notifying the notified body in case of any changes or revisions. An image from the "checklist" above.
REGULATORY TESTS
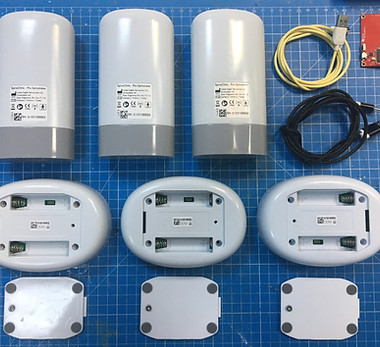
Electrical safety, transport validation, cleaning validation etc for regulation requirement. We had produced samples to send for tests. Then we reported the tests of the products and added them to the technical file. Prepare to be submitted for photo BLE testing from 3 sets of SpiroClinic Pro products.