
Our product, which we started selling in 2021, is "SpiroClinic Pro".
Carbon Health
Senior Industrial Designer
MAY 2022 - CONTINUING, ANKARA
We evaluated our products in the market in this range. We reviewed customer feedback and market research. We determined the deficiencies and improvement points on our product, planned the work to be done to correct them and distributed them to the departments. Then we tried to complete these goals.
The processes I contribute to;
Preparation of GAP Analysis on mechanical and brand issues of SpiroHome product family.
Work on improving part design to facilitate and speed up product assembly.
Improved part design prototyping and testing.
Design control for production.
Mold analysis for plastic injection production.
Packaging design improvement process.
Management of production, storage and stock control operational works.
PARTS TESTS

We made product improvement studies by analyzing after-sales support requests and technical service processes. As part of this, we worked on improving the way of product assembly and the chemicals used.
In the photograph, the durability of a bonding method used for assembly is measured with a newton meter.
PARTS ANALYSIS

We made waste and efficiency analyzes on our parts produced by injection molding. We researched, planned and started to implement ways to use the raw materials used more efficiently and to reduce production waste.
INJECTION PLASTIC AND MESH MATERIAL CONTROL
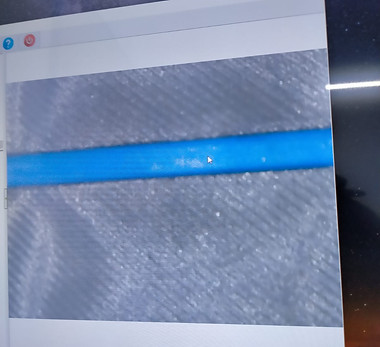
In one of our parts, we included a fabric-like filter directly in the mold for injection. We developed a test setup with a high-resolution microscope in order to understand the percentage of waste and to control the accuracy of the production. A certain percentage of each produced lot was automatically controlled by the direct injection printing supplier and the images were transferred to us.
PARTS TOLERANCE IMPROVEMENTS
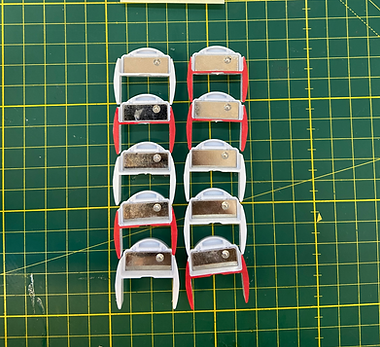
We made production tolerance improvements for each part that makes up our product. We reconsidered the relationship of each part to the other parts that it worked with mechanically and improved their design. Photo: From trying to tighten the rails of the product battery cover.
TECHNICAL SUPPORT

In line with the demands of the customers for the products put on the market, we have carried out the controls and tests of the customer products. We did the design and documentation of all these processes. We also received a technical service competency certificate.
PCBA ASSEMBLY DETAILS DESIGN
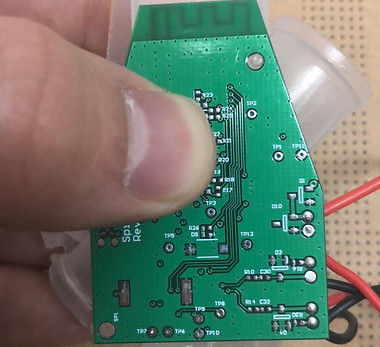
We revised the designs of some of the plastic parts as a result of mass production optimization. One of them was the inner part that held the PCB on it. Here, we have added various details on the part to speed up assembly and reduce product use-related breakage.
PRODUCT TRACKING

We had to follow every part and product as required by the regulations we followed. For this, we set up a barcode system before stocking products in mass production. The products produced were put in boxes of 20 before being taken to the warehouse, and the product serial numbers in each box were tracked through the system we set up. Thus, we were able to stock products safely and cleanly, and we were removing the process of checking one by one before shipping.
MOUTHPIECE IMPROVEMENTS

We made a double chamber injection mold for our Spiroway Reusable product. Since this piece contains the area where our Spirohome Personal product measures, it was very important that all mouthpieces be of a certain performance and identical to each other. We were producing with raw materials and injection machines in a controlled environment. We were constantly monitoring the temperature and humidity.