
Our "SpiroClinic Pro" product is the render we prepared for printed and digital promotional materials.
Inofab Health
Production Manager - Industrial Design Team Lead
NOVEMBER 2018 - SEPTEMBER 2020, ANKARA
In this process, which includes the COVID-19 pandemic, the company's sales increased in a very short time. Therefore, the continuity of mass production and increasing the production volume were of great importance for the company and we worked on it. We have also increased our infrastructure and human resources in this direction.
The processes I contributed in the position of Production Manager;
The process of transferring the output of the completed development process for the product to production.
Production of plastic injection molds for mass production.
Optimization of product assembly steps according to time / difficulty levels
Injection mold design, filling, cooling and shrinkage analysis.
Planning and implementation of post-production parts storage processes.
Planning and implementation of “sample production” before mass production with all stakeholders.
We kept master excel document for raw material, part and semi-finished stock tracking.
Designing and creating TDS (technical data sheet) for all parts in production.
Establishing and operating a version tracking system for all parts in production.
Determination of part technical quality control points, shapes and control percentages and design of the process
Coordinating between manufacturers
Creating a mass production assembly line.
Raw material stock tracking.
Raw material purchasing planning and post-purchase shipment and stocking.
The processes I contributed in the position of Industrial Design Team Leader;
Box and product label design according to relevant standards and regulations.
Design of product/part box and shipping boxes in accordance with relevant standards and regulations.
Design, manufacture and installation of common areas for the office.
Mechanical and Electronics lab design, production / assembly
Warehouse design for product and parts stocking.
Design of in-warehouse parts movements.
Product assembly area design.
Graduation project process with 3 industrial design students.
MASS PRODUCTION TRANSFER

Our increasing sales volume required us to increase our production capacity. We were trying to transfer assembly and testing processes to a company. For this, we gave trainings in the production area and transferred the production with our instructions.
INCOMING PARTS QUALITY CONTROL

In the first productions, I personally made the controls of the first batches in order to determine the shape, percentage and acceptance criteria of the part quality controls.
Afterwards, we documented the points that needed improvement and carried out pattern correction works. We also created the Input Quality Control Instruction with the controls here.
PART ANALYSIS
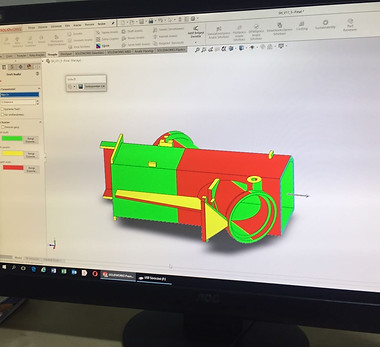
After completing the part designs, we made pre-molding controls. We were controlling the "surface relief angles" so that the part could come out of the injection mold.
In addition to these, we also made analysis of mold filling and part cooling.
WAREHOUSE MANAGEMENT

With the increase in production numbers, we kept a new office. We planned to use our new office as a production and assembly place.
For this, I first divided the office according to storage and assembly needs and designed its flows. Then, I designed the shelf system for the office and furniture for the ESD assembly line, and I personally followed the implementation.
RAW MATERIALS - PRODUCT TRACEABILITY

Due to the regulations we had to implement, we had to implement a high level of traceability.
For this, first part ref. We set up a code system. Then we designed suitable places for labeling on the parts and tracked each part by lot or serial number. We used to put serial number labels on the PCBA and store the test results of each PCBA in the serial number.
SAMPLE PRODUCTION

In order to adjust the part tolerances well, we produced parts with unpainted-transparent raw materials. In this way, we were able to closely examine the relations between the parts.
SAMPLE PRODUCTION

Before the mass production transfer, we produced samples in low numbers (50-100 pieces) for user and functional tests. We use our outputs in this process to determine the assembly method, order and time in production.
In addition, the draft version of the assembly instruction is also revealed.
PACKAGE DESING AND PROTOTYPING

I had prepared the prototypes of the packaging versions I designed with laser cnc using real materials. Then we simulated and validated the "transport validation" tests.
OFFICE INTERIOR DESIGN AND IMPLEMENTATION

I had designed the interior flow, partitioning and furniture of our new office. Then I personally followed its implementation.
FINAL ASSEMBLY ULTRASONIC WELDING

We experienced the use of ultrasonic welding in the final assembly of a part we designed. For this process, we used 3 different part molds and made the surface designs required for welding in the injection mold.
WAREHOUSE MOVEMENT FORM
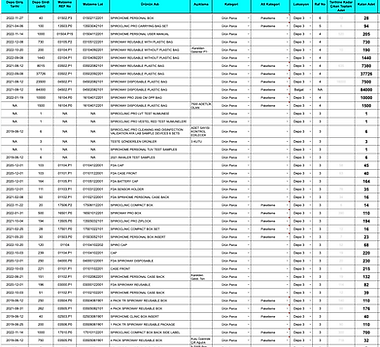
We were using a user-limited excel for stock tracking of raw materials and parts. We were following the lot and version of the parts in this excel.
INJECTION MOLD PRODUCTION

We were producing our parts with the injection molding method. We were producing with 7 molds for Spirohome Personal. We also worked closely with the manufacturer during the molding phase. Mold runner design, cooling channels etc. We did simulations on all the details.